Most consumers have no idea how technical it is to be able to mount/demount tires. The more you know, the more involved the process becomes. Take the physical act of mounting and demounting a tire. This process involves two to three times more steps than the average consumer realizes and, unfortunately, more than many tire dealers don’t get credit for performing them.
As a case in point, I was recently helping out a gentleman with a tire that was low on air. He had an emergency and needed to leave work in a hurry. I assumed that there must be a puncture, but I was hoping to just air up the tire enough to get him rolling until later in the day. I quickly realized that the air was leaking around the bead area and wasn’t going to hold to get him to the hospital. I quickly air-bag jacked the truck and removed the assembly, hoping for a quick repair that might require cleaning only the bead area to remove debris. After removing the tire, I saw rubber buildup on the bead area of the wheel, which I buffed off with a wire wheel. Upon closer inspection, I found two cracks on the rear flange (see Photo 1). At this point, I stopped the process and informed the customer. We decided to install the spare to get him on the road and, in the meantime, I started to source an OE take-off wheel for him.
This leads to an important question that we all need to ask ourselves, “Are we billing enough labor for our team to have the time to do the type of inspection that should occur on each job?” A customer who was watching me install his new tires, told me that he had never seen anyone spend so much time prepping the wheel before the tire was actually mounted. I had removed the old tire, buffed the bead seat areas clean of debris, inspected the bolt holes and flanges, and then buffed the mounting pad to prevent joint settling. This is the condition that can occur over time when dirt and rust fall out from between the wheel’s mounting pad and the vehicle’s hub, which can lead to the lug nut torque diminishing over time. As mentioned in previous articles, I want to bring to light a number of areas where we can not only improve profitability, but also improve the value of the services that we provide. One such area is the during demounting/mounting process.
To properly dismount and mount a tire, there are a number of processes that must be followed. TIA has done an outstanding job with its ATS program, but there is more to learn, so let’s get started.
WARNING! Never assume the tire or wheel on the vehicle is correct unless they are the original equipment (OE). Perpetuate someone else’s mistake of installing the wrong tires and you are married to this vehicle and any consequences that arise from touching it.
- Test Before You Touch. Check the TPMS telltale light to see if the bulb is good and then goes off, indicating that the system is functioning. Next, directly check the sensors with a proper scan tool.
- Inform the vehicle owner if any lights are on. Remember, indirect systems rely on the wheel speed sensors to detect low tire pressure. If the ABS light is on, then traction/stability control and tire pressure are not being monitored.
- Is the current tire correct for the vehicle? Check to see that the tire size, construction type, load index/load rating, and performance/speed rating match OE specs.
- Is the tire non-OE? Check to see that the tire size, construction type, load index/load rating, and performance/speed rating meet or exceed OEM specs. Use a Load and Inflation table to determine if the non-OE tire will carry the load and, if so, at what air pressure. Also, does the tire-approved rim width fit the wheel? Hint: LT285/70R17 does not fit on an OE dually wheel.
- Is the wheel OE or aftermarket? If OE, proceed to 7.
- For an aftermarket wheel, is the width and offset too aggressive and causing the tire or wheel to rub on the vehicle body or suspension?
- Verify that the tire to be installed is correct, such as LT-metric instead of Euro-metric for 3/4-ton and heavier trucks, etc.
- Use only a breaker bar and socket to loosen lug locks or spline drive lugs. Never use impact guns.
If there are no issues, work on the vehicle can begin.
1. Check the ALI Lift Guide to find out where to pick up the vehicle and turn off any active suspension systems.
2. Carefully remove the tire and wheel assembly.
3. After deflating the tire, use your tire changer to break the tire beads loose using the proper tools and techniques for your equipment.
4. While depressing the tire bead, check for a band sensor. Remember, there are still mid-2000s Ford/Lincoln/Mercury vehicles with band sensors that are secured 180 degrees from the valve hole (see Photo 2).
5. Also, look for the position of the drop center to determine whether the wheel is standard drop or reverse drop (see Photo 3). The reverse drop has to be face down and clamped from the outside using plastic protectors over the metal clamps to prevent damage. Center-post changers, such as touchless machines, will require the reverse adapter with pins to align through the lug holes. Please share this information with your team. I constantly see dimples on the face of wheels (see Photo 4).
Getting Ready to Dismount
- Lube up the tire beads and wheel flange to ease the tension between the two pieces.
- Position the TPMS sensor, or regular valve stem if not equipped with a sensor, under the demount head.
- Slide the pry bar under the top bead and unfurl it by reversing the turntable in a counterclockwise rotation for a couple of inches.
- Now, rotate the turntable clockwise to allow the top tire bead to slip over the wheel flange.
- Re-index the sensor or valve stem and pull the bottom bead off of the wheel.
Follow these steps to prepare to reinstall the new tire.
- Clean the bead seat on the wheel with a wire brush or wire wheel.
- Examine the flanges and lug holes for cracks or bends.
- Examine the spokes on the face of the wheel for any cracks.
- Swap out the rubber valve stem or rebuild the clamp-in aluminum TPMS valve stem with a new service pack. Remember to torque to spec, according to the specific pack. Ranges are typically from 35 in.-lbs. to more than double that. Get it wrong and you will be buying a sensor or have a leak. Use calibrated tools, not just a ratchet.
- Lube up the wheel across the barrel and bead seats, as well as the tire bead seats and the underside innerliner of the top bead, so that it slides over the wheel flange without binding up.
- Most importantly, place the TPMS sensor ahead of the “traction point,” which is where the tire bead crosses over the wheel flange.
- Once the tire is on the wheel, seat the beads with no more than 40 psi, unless the assembly is in a restraining cage, while following manufacturer guidelines. WARNING: If you are installing steel sidewall tires, place them in a safety cage and follow RMA or TIA guidelines for inflation.
- Once the beads have been seated, deflate the tire to allow the bead to relax and settle on the wheel bead. Why? The tire bead has to slide over the safety humps on the wheel that cause the tire to have an artificial high spot that can lead to vibration not caused by imbalance, if you miss this step.
- Inflate the tire to either the recommended air pressure front/rear if it’s an OE application, or calculate the proper air pressure needed if the tire is not OE. If that is the case, place a new door placard on the driver’s door jamb with the correct air pressures.
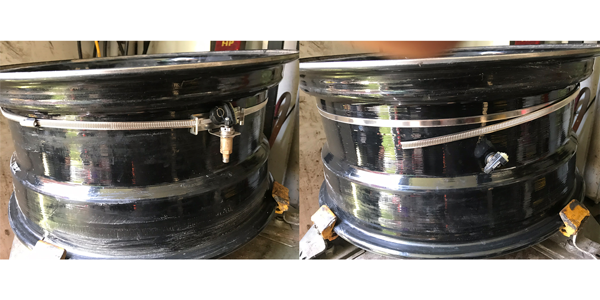
This is a tried-and-true procedure that will greatly reduce the chances of damaging the tire, wheel or sensor. Speaking of sensors, I had to convert a six-wheel F-350 built as a Firetruck into a four-wheel Brush Truck with mud tires. So, how did I make four rear TPMS sensors work in just two wheels? I put the outside rear sensors in the valve stem holes and used an aftermarket band and cradle to mount the other TPMS sensor at 180 degrees away (see Photo 5). Both sensors are sending the same information and function without any issue.